How proper humidity control saves you money when increasing ventilation
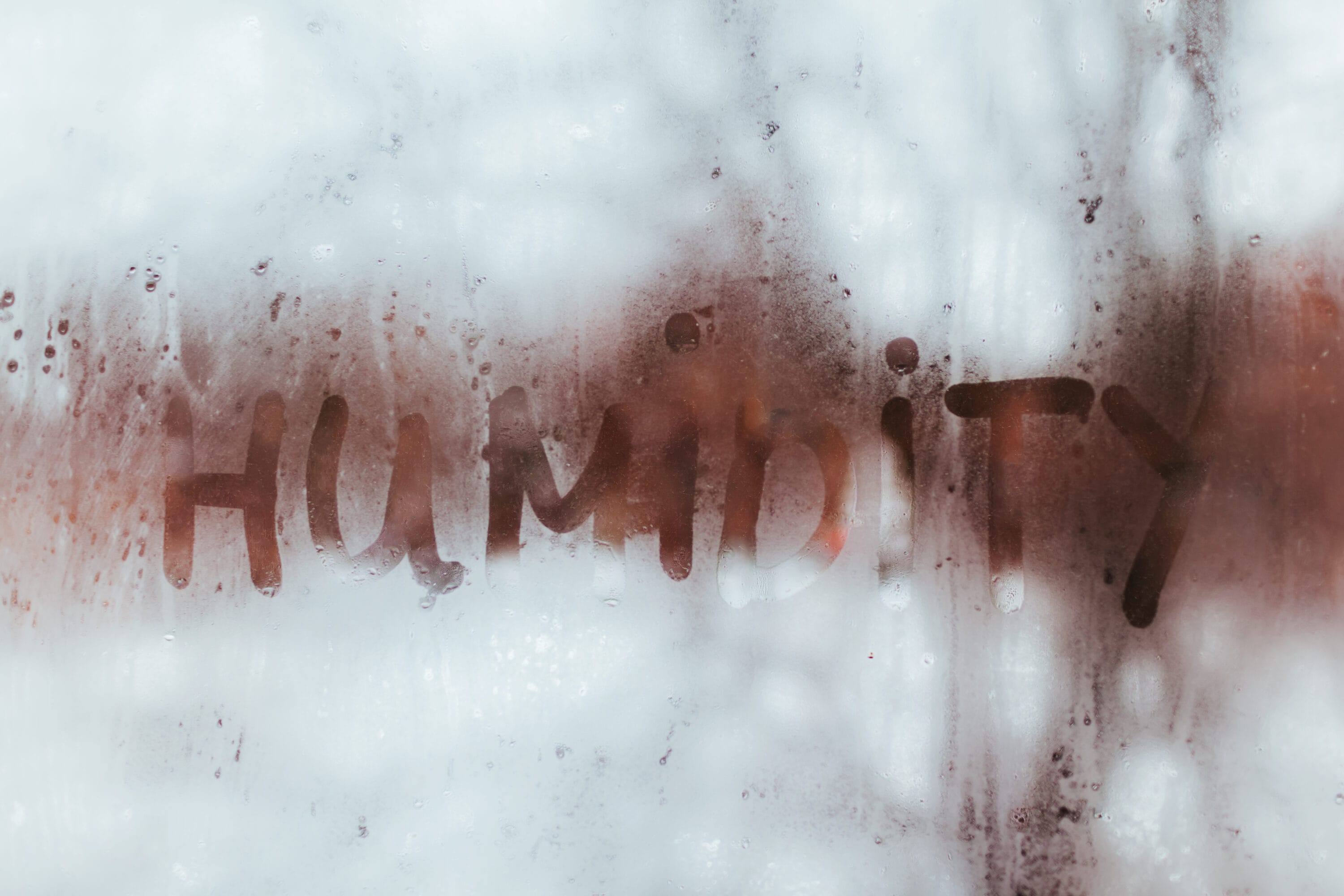
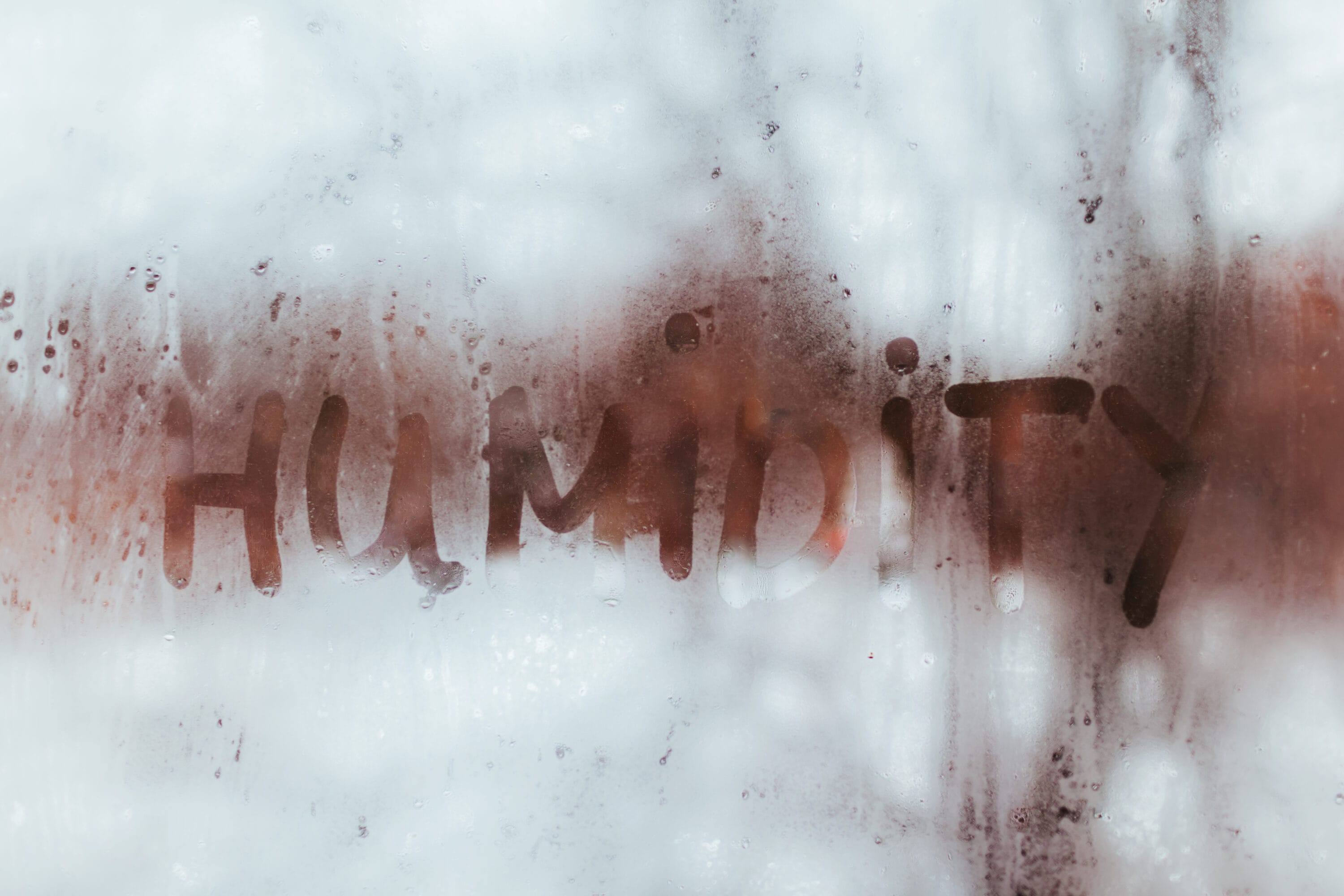
If you run a business – regardless of the industry – it’s no secret that increased ventilation has become a hot topic since the pandemic took hold earlier this year. But, are you prepared to handle dramatic shifts in humidity that can affect everything from products and customer comfort to your energy bill – all due to an increase in fresh air intake from outside?
Consider the spike in humidity an unintended consequence of trying to do the right thing. You want to increase ventilation in your building, because the science shows exchanging air helps reduce the amount of COVID-19 floating throughout your building. That, in turn, should theoretically keep your facility safer for employees and visitors.
So, let’s break down the challenge, potential solutions, and how one relatively unknown solution can save you money, headaches, and time.
Increasing ventilation: the background
So we’re all on the same page, let’s start with how this need for drastic ventilation came to life.
Earlier this year, the Centers for Disease Control and Prevention (CDC) released facility guidelines that indicated increasing outdoor air ventilation and total airflow could dramatically reduce COVID-19 susceptibility. While ideal on paper, it’s nearly impossible – or at least unrealistic – for most facilities.
Shortly thereafter, Minnesota mandated that grocers need to use 100 percent outside air. This meant they couldn’t recirculate air inside their facility. Simple to do but the impact is severe. The result is costly and inefficient when it comes to consistently maintaining comfortable and safe temperature and humidity levels.
Since then, businesses of all sizes have followed suit, prioritizing ventilation. While not an issue in the short-term, the approach isn’t sustainable long-term, due to high energy costs and challenges stabilizing temperature and humidity.
The common solution And why it doesn’t work.
To increase ventilation so dramatically, facilities have to set air handlers to use 100% outside air. That means no air is recirculated through the machine. Therefore, the air handler only gets one chance to knock down temperature and humidity.
Under “normal” circumstances air is recirculated, allowing the units to knock the temperature down and remove more moisture from the air each time it passes through. That helps create stable temperatures, and decent humidity control and it’s relatively efficient (compared to using 100% outside air).
So, why is that such a problem?
A couple of reasons:
- Air handlers aren’t designed to operate this way. They’re horribly inefficient when they only get one pass at the air. They consume tons of energy, which causes bills to skyrocket.
- It’s only moderately effective. Yes, air exchanges are occurring at an increased rate, but because of varying outdoor weather conditions, it’s more difficult to maintain consistent indoor air quality. For reference, ASHRAE recommends 40-60% relative humidity (RH) in its indoor air quality metrics.
In some instances, we’re seeing facilities add an additional refrigerant-based rooftop unit/air handler to help. Or – and this is a slightly better option – operators are adding a dedicated outdoor air system (DOAS). Both options are costly. The easiest way to look at the potential cost is to think of it in dollars spent per ton:
- Generally, 3-ton machines cost about $1,500 per ton.
- Larger machines (25 ton) cost about $900 per ton.
- Adding reheat coils (inefficient ways to remove humidity) is an additional $1,000 for a 10- to 15-ton unit.
Most importantly, in isolation, neither of these approaches offer the most efficiency and cost savings.
Dehu + DOAS + air handlers = savings and stability
Wait, more machines and you’re telling me it’s the best option? To channel our Midwest roots: You betcha.
Here’s why: When each unit is doing what it’s designed to do, performance and efficiency improve. It’s like letting your quarterback focus on quarterbacking, rather than having him block and play defense as well.
Here’s why: When each unit is doing what it’s designed to do, performance and efficiency improve. It’s like letting your quarterback focus on quarterbacking, rather than having him block and play defense as well.
The easiest way to look at this is in an example:
- For the sake of the argument, we have a 10-year-old store with existing air handlers.
- We would then add a DOAS unit to handle 100 percent of the ventilation responsibilities. This is what it does best.
- Then, reconfigure your air handler to recirculate 100% of the inside air. Generally, they’re set to include 10% outside air, but that reduces efficiency. Remember, air handlers are best at handling the sensible load. Again, more efficiency.
- Lastly, add 2-3 500-pint commercial dehumidifiers inside the facility. These will handle the latent load. An added bonus is each machine has a filter on it, meaning you’re capturing contaminants that might otherwise be inhaled by occupants.
With this option, you’ll see a significant reduction in energy costs as well as capital investment. Generally you’ll see about a 26% decrease in operating costs and 32% savings in capital expenditures.
With this option, you’ll see a significant reduction in energy costs as well as capital investment. Generally, you’ll see about a 26% decrease in operating costs and 32% savings in capital expenditures. If you’re interested in learning more or in seeing how the calculations play out in your facility, send us a note or call any time.
About the Author
Walt Waetjen is a senior product manager at Quest. He specializes in helping organizations find the most efficient, effective solutions for their environmental control challenges.